Most businesses in high-risk industries like construction or manufacturing have safety procedures and policies. But what makes a “safety program”? Do you need one? And how does putting safety first impact your business?
In this guide, we’ll cover the following points and in the coming weeks, POWERS will continue to post additional deep dives into each of the below topics. You can find all POWERS Research and Industry insights here.
- Why every business needs a workplace safety program
- How to Build a Safety Culture (or Make Yours Even Better)
- How to Identify Hazards with a Risk Assessment Framework
- Safety Program Development: How to Create and Implement Policies
- Reporting and investigating incidents
- Measuring success: Which KPIs to track
- Top safety policies for any business
- A successful safety program takes a village
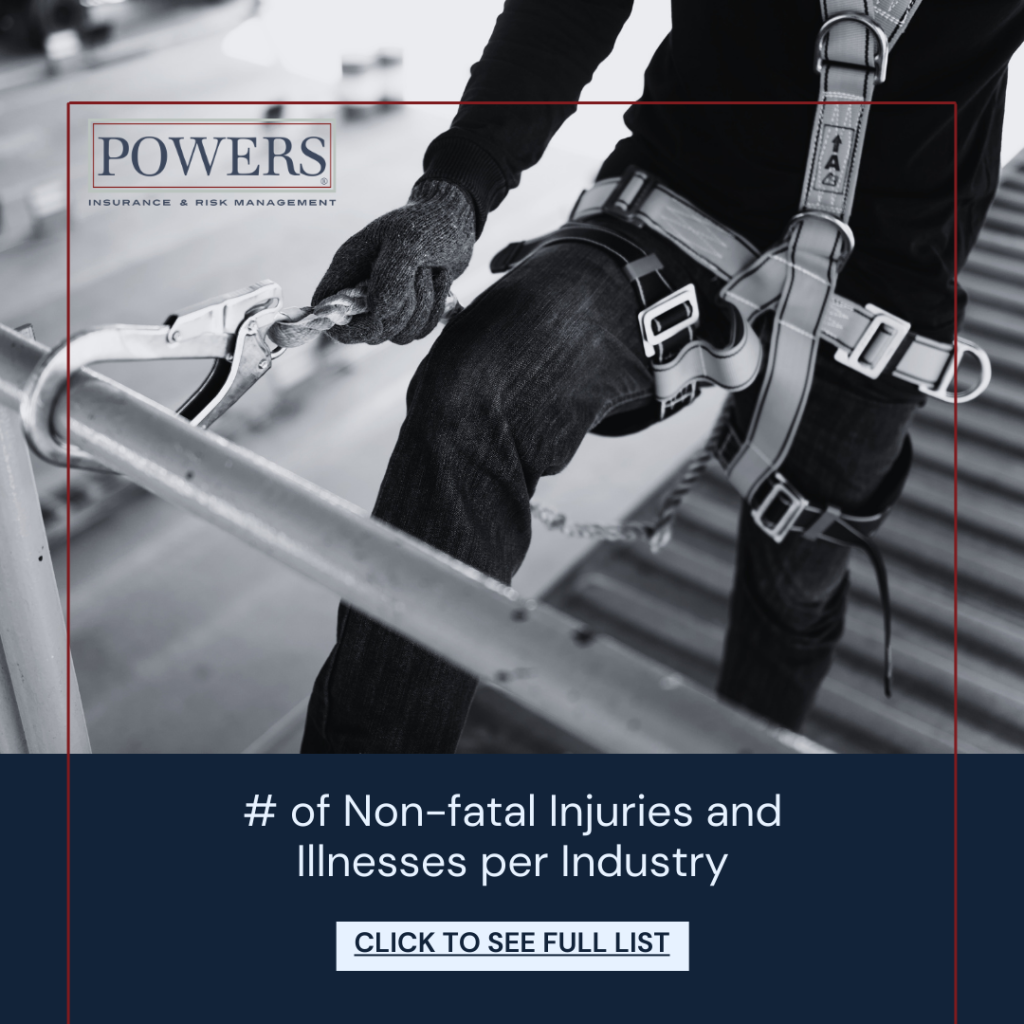
Why every business needs a workplace safety program
Do you need a formal safety program in a lower-risk industry like professional services? In 2021, there were 2.6 million work-related injuries and illnesses in the U.S. About 10% of them happened in perceived low-risk industries.
Incidents happen in every sector. There’s not a business out there that doesn’t stand to benefit from implementing a safety program or improving its existing one.
Compliance matters
As a business owner, you have a legal responsibility to provide a safe work environment. The U.S. Department of Labor provides detailed standards, rules, and regulations to follow.
Your legal obligations:
- OSHA standards: Safety requirements by industry covering hazard communication, PPE, machinery and equipment safety, electrical safety, and more.
- General Duty Clause: Requires employers to provide a safe working environment free from recognized hazards. This clause covers potential hazards not explicitly discussed by existing safety standards.
- Recordkeeping and reporting: Requires employers to maintain records of work-related injuries, illnesses, and fatalities, and report certain incidents within specific timeframes.
Benefits of safety – and costs of incidents
The ultimate benefit of a safety program is that it protects your employees. You can’t put a number on the value of saving lives.
However, this perspective often leads leaders to think of a safety program as a cost center rather than an investment with a concrete return.
Instead of asking about the benefits of safety, the more impactful question is:
What is the cost of an incident?
Keeping your employees safe isn’t just about right and wrong – it’s also about dollars and cents.
First, there are the direct monetary costs to your business when an incident happens. These hard costs include:
- Out-of-pocket costs like medical expenses, property damage, and legal fees
- OSHA fines ranging from hundreds to tens of thousands of dollars
- Increased workers’ comp premium due to high claim frequency or severity
Most business owners know the hard costs of incidents, but many don’t consider the soft costs. These indirect costs add up over time and erode your business’s profitability. They include:
- Decreased productivity from downtime and distraction
- Higher turnover as employees look for safer jobs
- Lower engagement and morale
- Damaged reputation and trust that harms retention and new business
Return on investment in safety
While it’s difficult to quantify the dollar amount saved by preventing incidents, understanding the potential costs helps contextualize the return on investing in safety.
Your ROI could include:
- Reduced hard costs related to incidents
- Improved productivity and efficiency
- Higher employee morale, engagement, customer trust, and brand loyalty
Now that we’ve covered the potential returns, you might be wondering:
What’s the investment?
According to Safety+Health’s latest training survey, 60% of companies spend more than $200 per employee per year on safety training. However, you may be able to offset some of those costs by outsourcing safety support, or using resources from your insurance carrier or agent.
Getting started: How to establish a safety culture
Why start with culture? The best safety policies in the world won’t make a difference if your employees don’t think you mean it.
To foster a safety-first culture, you need three things:
- Leadership commitment
- Employee buy-in
- Enduring consistency
1. Leadership commitment
Your company’s commitment to safety starts at the very top. That means top leadership should be publicly discussing safety on a regular basis.
Of course, talk will only get you so far. Your employees will also need to see action, like:
- Leading by example: Follow safety rules every time
- Prioritizing safety over productivity: Create space for bringing up concerns
- Investing in safety: Budget for repairs and replacements before they’re critical
Safety shouldn’t be a compliance checkbox with no practical follow-through. It should be a true core value, in public and behind closed doors.
2. Employee buy-in
Although a positive safety culture may start as a top-down initiative, you need employee buy-in to keep the momentum.
Some ideas to get employees involved:
- Encourage hazard and near-miss reporting by providing multiple channels, including online, paper forms, and face-to-face.
- Ask tenured workers to share their own safety stories or advice during team meetings.
- Form a safety committee with employees from a variety of roles and functions.
- Recognize and reward safe employees. Be sure to focus on proactive safety measures and incident reporting, as rewarding “zero accidents” can incentivize employees to hide workplace hazards or incidents.
3. Consistency is your master key
Implementing 25 new rules, procedures, meetings, and incentive programs tomorrow will be overwhelming for employees and unsustainable for company leaders.
If you’re beginning with a very basic or nonexistent safety program, start with the fundamentals, such as:
- Communicate the importance of safety to employees
- Identify and address your company’s top 3-5 safety hazards
- Put your top 3-5 safety policies in writing and have employees sign them
Above all, maintain consistency in your implementation. The rules must apply to every single person, every single time. Over time, employees will see that this is your new way of doing business.
Assessing your risk: How to identify top hazards
You might think you know your top risks without a formal exposure analysis; so why do you need to do a risk assessment?
The most obvious hazards aren’t always the most impactful. Since enforcing safety policies takes effort and resources, you want to make sure you’re focusing on the right areas.
At POWERS, these are the four foundational steps we use to protect our clients.
- Identify and assess risks
- Implement risk strategies
- Plan your response to risk events
- Monitor risks
1. Identify and assess risks
Review your company’s past claims, incident reports, near misses, and anecdotal perspectives from a variety of team members.
Next, your goals are to prioritize and devote resources to controlling the most important risks.
There are two factors that determine a risk’s importance: probability and severity. Look at the list of risks you identified and answer two questions for each of them:
- Probability: What is the likelihood that this risk will happen?
- Severity: What are the potential costs if it does?
2. Implement risk strategies
Once you’ve prioritized your top risks, decide how your company will approach each one. There are four types of risk mitigation:
- Avoid the risk altogether
- Transfer the risk to another party via contracts or insurance
- Mitigate and minimize the risk as best you can
- Accept the risk and its implications
For most of the exposures you identify, options 2 and 3 will be most appropriate. Here are some steps that can be taken to mitigate these risks:
- Train employees on your company’s safety, security, and risk response policies.
- Post compliance standards and safety policies where everyone can see them.
- Create contingency plans so you’re prepared to respond to an incident.
- Get the right insurance policies to transfer the financial burden to your carrier.
3. Plan your response to risk events
One of the most important parts of risk management is being prepared to act if a risk event does occur. Some risks are unavoidable. For example, no one can prevent natural disasters – the best we can do is be prepared.
Your risk response plan could be as simple as “file an insurance claim.” But the higher priority the risk, the more detailed your response plan should be. If an event has the potential to disrupt business operations in a huge way, business continuity and disaster recovery plans are essential.
It’s crucial to make these plans ahead of time. Because when minutes matter, you won’t have time to deliberate.
4. Monitor risks
Doing a risk assessment once and letting the report collect dust will not help you protect your business in any tangible way.
It’s vital to monitor your company’s risk profile as it evolves and make sure your responses are still appropriate. Repeat the steps of this risk management plan regularly.
Dig in: OSHA compliance |
Developing a program: How to create and implement policies
When it comes to creating policies, there’s no need to reinvent the wheel – don’t be afraid to lean on others’ experience and expertise.
There are hundreds of templates online. Start by looking for resources specific to your industry from reliable sources such as trade associations or insurance carriers. Then, customize the resources to fit your company’s unique needs.
Establishing safety policies
It’s important to document your safety policies and procedures. Don’t rely on verbal agreements or procedures passed down through training alone. Everything should be signed by employees and easily accessible.
While the policies you create depend on your industry and risk assessment, here are some ideas for where to start:
- Create a comprehensive safety policy stating the company’s commitment to safety and confirming employees’ agreement to put safety above all else
- Define concrete expectations for employees around what it means to put safety first
- Address key, general areas like your incident reporting process, emergency procedures, and proper usage of PPE
Creating standard operating procedures
Standard operating procedures (SOPs) are step-by-step guides to safely doing specific jobs. These documents should detail the following:
- Required equipment and tools
- Required PPE
- Required competencies
- Specific maintenance and usage guidelines
SOPs are meant to be detailed. Write them for a new employee performing the task for the first time, without assuming prior knowledge or experience.
To create relevant SOPs, involve the employees who do the task. Ask for employee input from the beginning to avoid SOPs that are too theoretical or generic.
Then, set reminders to review and update SOPs in case the process or equipment changes.

Educating employees
Amazing procedures don’t matter if your employees don’t follow them. Here are our top tips for safety education that stick.
- Train every employee on new policies and SOPs, then add them to your onboarding process for new employees.
- Ask employees how they prefer to learn. If possible, offer different options, such as a classroom setting or an online session.
- Document who completes training and have employees sign safety policies. Documenting sign-off is important for both compliance and making employees feel personally invested in follow-through.
- After the initial training, communicate policies regularly through a variety of channels, such as safety meetings, toolbox talks, posters, and emails.
Reporting and investigating incidents
If a workplace accident happens, the most important thing is to understand what happened so you can prevent it next time.
How do you do that? By encouraging incident reporting and investigating each incident.
Establishing an incident reporting system
If there are roadblocks to reporting or if employees think there could be negative consequences, they will be less likely to report incidents or unsafe conditions.
That’s why it’s important to create a reporting process and communicate your intentions to employees. Emphasize that the point of incident reporting is not to place blame, but to prevent similar incidents in the future.
Our best advice for successful incident reporting:
- Document processes for reporting incidents, near misses, and hazards.
- Make reporting accessible by providing multiple channels, such as online, paper forms, or face-to-face.
- Give clear timeline expectations and emphasize the importance of timely reporting.
- Let employees know that reporting can be confidential if they wish.
A lot of sample reporting policies and forms are online. Search for the ones that best fit your needs and don’t forget to customize them if needed.
Incident investigation process
When an incident happens, a quick investigation is paramount. That’s why it’s important to have your investigation process ready to go when you need it.
Incident investigation pro tips:
- Designate a person or team responsible for investigating reported incidents.
- Provide training and resources on evidence collection and witness interviews.
- Emphasize that the investigation should be conducted as soon as possible before the scene is disturbed or witnesses forget what happened.
Corrective action: Fixing the root cause
All incident investigations should focus on root cause analysis. That means digging beyond the surface-level cause of an incident to identify if and when your safety program failed.
Some common root causes of incidents:
- Safety policies are not clearly communicated
- Policies are not consistently enforced
- Training is inadequate
- Company culture normalizes fatigue or distraction
- Safety equipment and PPE are not adequate or conveniently located
Identifying the root cause, not punishing an individual employee, will help you prevent future incidents.
Follow-up: After the investigation
An incident investigation will give you valuable information. To put that info to good use, communicate your findings and subsequent changes to all stakeholders, including employees. Turn an unfortunate incident into an opportunity to learn and teach.
Measuring success: Which KPIs to track
Mathematician Karl Pearson said, “That which is measured improves.” If your goal is to improve your safety program, you must track key performance indicators (KPIs) to measure its efficacy.
Establishing KPIs: What should be measured?
The metrics most companies track to measure safety performance fall into two categories: lagging indicators and leading indicators.
A lagging indicator is a metric that changes after the variable it measures changes. For example, if your company tracks a safety incident rate, you’ll see the rate increase after the number of incidents increases.
Common lagging indicators for workplace safety include:
- Recordable incident rate
- Lost-time injury frequency rate
- Lost-time injury severity rate
- Near miss rate
Lagging indicators function as a final “cry for help.” In a perfect world, safety pros would also track metrics that help identify safety concerns before they turn into workplace injuries. These safety metrics are called leading indicators.
Common leading indicators include:
- Safety training completion rates
- Safety meeting participation
- Safety audit scores
- Equipment maintenance records
- Operational bottlenecks
How to monitor and track safety
Standardization is the best way to measure your chosen KPIs without feeling overwhelmed or overcommitted. Here are some tips:
- Standardize safety audits with checklists. Look for templates from trustworthy sources online, and tailor them to your organization’s needs.
- Have a plan for corrective action if your audit reveals a worsening KPI or one that falls below the benchmark.
- Consider safety management software to streamline auditing, tracking, reporting, and implementing action plans.
Analyzing incident and near-miss data
Having an incident investigation process is key to identifying root causes and applying preventive measures. If your KPIs reveal trouble in a particular area, review the relevant investigation reports and look for patterns.
The further you dig into the underlying causes of the troubling metric, the more targeted and effective your interventions can be.
Employee feedback and engagement
The best systems for continuous improvement include both quantitative and qualitative inputs. Don’t forget to involve your employees every step of the way.
Devote significant effort to developing and maintaining a strong safety culture. This opens feedback channels to help you gauge employee perceptions of safety, training effectiveness, and management’s commitment to health and safety.
Top safety policies for any business
Ready to put pen to paper and document your safety policies? Every business has different safety needs, but here’s a list of policies and procedures to consider for your workplace safety program.
General safety policies
- Agreement: Safety is our number one priority
- Incident reporting policy
- Near miss reporting policy
- Safety training policy
- Safe driving policy
Emergency preparedness
- Lockdown/violent intruder response plan
- Severe weather response plan
- Fire response plan with evacuation map/emergency exits
- Medical emergency response plan
- First aid, CPR, and AED training policy
Housekeeping and organization
- Clean and orderly worksite guidelines
- Spill control and cleanup policy
- Handling procedures for hazardous materials and toxic substances
Personal protective equipment (PPE)
- List PPE required for all jobs
- Process for requesting new safety gear
- Proper PPE use and maintenance guidelines
Ergonomics
- Workstation design and correct posture
- Safe lifting techniques
- Job rotation policy to minimize repetitive motions
Slips, trips, and falls
- Fall protection policy for safety harness use
- Guidelines to avoid slips and trips
- Working at heights safety guidelines
Machine safety
- Job-specific Standard Operating Procedures
- Lockout/tagout system
A successful safety program takes a village
Preventing injuries is an investment worth making. However, those resources can quickly add up. Explore your options for outsourcing safety support where you can. Does your workers’ comp carrier provide resources? How about your agent?
All POWERS clients have access to in-house experts to help with:
- Safety education and program development
- Exposure analysis
- Loss control analysis
- OSHA Compliance
- Contract alignment review
- Workers’ comp e-mod forecasting
It’s all about helping you protect your people and reduce insurance costs without huge expenses.